



A Family Business
At The Weaving Shed we are a close-knit family business, I'm Miriam Hamilton (teasingly called the dictator by the others!) and with my husband Paul Robinson we started up our wee business back in 2018. We also have two crofts and run around 50 sheep. When I had our daughter Rosie, my sister Martha joined the team, and my brother John periodically roped in to help with croft work. Our sister Mary is now a vital part of the business too and is hoping to learn to weave over the winter. Martha's partner has also done fencing and other croft work and we joke that I'll end up employing the whole family eventually!
We are in the process of renovating a 150yr old stone cottage which we hope to rent out as a holiday let from spring 2025
Three Sisters Tweeds
To be called Harris Tweed the production of the fabric has to be carried out solely in the Outer Hebrides. The spinning, weaving, washing and finishing all has to be done here, although the wool itself doesn't come from island sheep. However for the independent single width weavers there was only one mill that was willing to sell us yarn and wash our cloth, and this became more and more unreliable. When our tweed had been there for over a year without being washed it became financially unviable to weave Harris Tweed. We decided to become completely independent, weaving our handwoven cloth under the brand Two Sisters Tweeds. Our fabric is washed and finished in Galashiels which gives us far more scope and variety in our choice of yarns and colours.
We weave with pure blended wools, supersoft lambswool, Shetland and luxury unusual yarns, including ones from my own sheep fleeces, alpaca-silk and undyed British breeds. You can find out more about our luxury tweeds HERE
My sister Martha weaves the tweeds we design together, I then create or design the majority of what we sell in the shop. We are now THREE Sisters Tweeds as my other sister Mary joined the businesses and makes the lampshades, buttons and helps out with other aspects of running the business!


The Looms
Hatty my Hattersley loom. Originally brought to the island as a brand new flatpacked puzzle in (about) 1940 she has been worked by three generations for over 85 years. Crafted from cast iron and wood she has become a work of art in her own right. The divots on the arms as she has settled into position, the wear on the bar from years of weavers hands, the faded paint and oil deposits. All help make each Hattersley loom unique and give them their own personality. Martha also has a Hattersley at her house, called Hetty, who is about 10 years older than Hatty. The two looms give us the flexibility to have different draft patterns set up on different looms, plus a backup if one breaks down! We also have a huge wooden Glimakra floor loom perfect for weaving thick floor rugs!
Two Sister Weavers
I purchased Hatty in 2018 from 89 year old retired weaver, Calum Iain from Kirivick, Carloway who very kindly agreed to sell me the loom and teach me to weave! I spent many hours in his tiny, freezing cold loom shed where he had woven for 50 years. He had inherited the loom from his father, who had bought her originally from the Hattersley factory in Keighley, Yorkshire in 1940. I taught my sister Martha to weave in 2019 and now she is planning on teaching our other sister too!
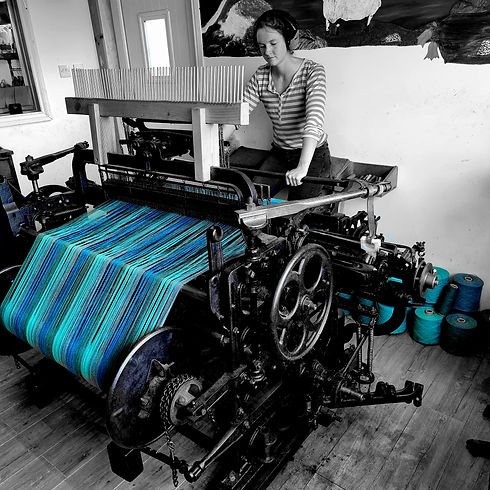
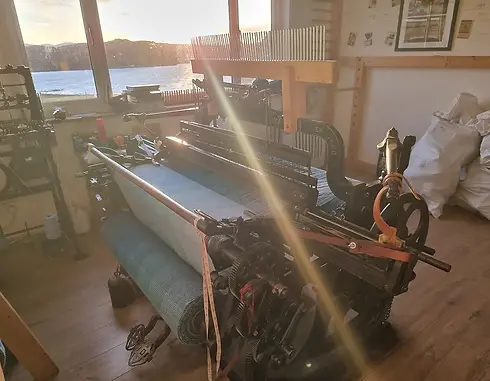
The Shed
Traditional weaving sheds, like the one I learnt to weave in, were block or stone structures with no real 'comforts' like insulation, decent lighting, heating etc. I decided I wanted a 'posh' shed and so The Weaving Shed was created. Designed in two halves; one to have exactly the right amount of room for Hatty, the pirn winder, the warping frame and the bobbin stand and the other as a studio shop. The 'posh' shed has stunning views over Loch Leurbost, and plenty of space and light to see the loom and all the weaving processes. The other half is my wee shop selling all my handcrafted creations.
A wee video showing some of the processes involved in creating the a tweed! If you don't like the music, mute it then unmute at the weaving part to hear the sound of the loom.
To actually make a tweed from start to finish takes several months from raw fleeces to finished cloth.
Once the sheep have been sheared and the fleeces picked clean of vegetable matter and poop, they are sent to the mill for spinning. First the raw wool is put into a machine that gently submerges and withdraws it from the water gradually moving down the belt as the water gets dirty meaning it uses less water overall. The fleeces are then dried and, once completely dry, picked and separated before being fed into the carding machine. Here it gets drawn through lots of rollers which brush the fibers into alignment. It comes out as a soft fluffy rolag and is stored in large drums. The rolags are fed into another machine that spins them into yarn.
Once back with us we need to turn the yarn into cloth.
First we have to make the warp. Between 6 and 24 cones of yarn fit on our bobbin stand, the threads are drawn off and wrapped around the warping frame on the wall. Each series of wraps gives the total finished length of the tweed. We normally weave around 60 meters, for the gotland it was 20. So depending on the number of threads used its anything between 29 to 116 wraps.
Once all wrapped the warp is chained up to keep it tidy, then beamed onto the loom.
The final step is tying 696 knots to join the old and the new warp together so the warp can be pulled through the heddles onto the loom ready to weave!
Before we can start weaving we have to wind the pirns using the other machine we have in the corner. These go inside the shuttles and cary the weft through the warp to make the cloth.
When each peddle is depressed that turns the lower shaft. That turns the teardrop shape cams which causes the picker arms to fling inwards, driving the shuttle. The lower shaft has a cog afixed to it which turns a larger cog attached to a block of cams. These control the heddles (the metal reeds in wooden frames) causing them to be raised or lowered in a set order. This raises or lowers the warp threads in a set order to create the 'shed' the shuttle flies through. That is the gap in the warp created by the heddles lifting different threads up in turn. This creates the over/under/over/under weave of tweed. We can change the order of the threads to get different weaves e.g. herringbone, twill, honeycomb, basketweave etc.
The lower shaft also turns the arm which controls the complex series of cogs on the righthand side of the loom that pull the fabric through the loom at exactly the right speed as it is woven. On each side of the loom are two large wheels, these turn the top wheels which turns the top shaft. That pushes the beater in and out every shot (press of a peddle) to beat the cloth to the correct tension. On the left hand side of the loom is a very complicated series of rods and cams that should control which way the shuttle box turns and how frequently. We have disabled ours however to put less stress on the loom after our lower shaft snapped twice!
Once the weaving is finished it gets pulled off the loom, folded into a bale and gets sent to a mill in Galashiels where it goes through a number of finishing processes. First it is washed, drawn through giant rollers that beat the cloth causing it to shrink (full) and bind the individual yarns together. This gives the cloth its strength and durability. Then it is stretched to its finished width and drawn flat through a drier to set the tweed. Then it is drawn through another machine with fine blades that crop the surface leaving it smooth and fluff free. Finally it is pressed and measured and sent back here!
Two Sisters Tweeds
You can now browse the website to buy either ready made products or fabric sold from the quarter meter
so you can order as much or as little as you want!
Weaving to Order
-
-
We are always happy to discuss weaving commissions. We can weave with your own yarn spun from your sheep's fleeces or we can design a tweed together based on yarn from our suppliers. We require a minimum order of 30 meters and can weave these main pattern styles; a block check, patchwork, multicolour warp, over check or a combination of the above. We can't weave tartan/plaid, houndstooth or complex checks due to the age and limitations of our 85 year old looms. For an idea of styles available please see our tweed range or previous works.
-
-
Tweeds are £40 per meter if you supply yarn and from £50 per meter if we supply the yarn depending on the cost of the yarn chosen. This price would be for supersoft lambswool or Shetland. We can also offer merino, heritage natural undyed and more!
-
-
If you are going to have yarn spun for us to weave with please confirm with us first the quantities, yarn weight and colours as otherwise we may not be able to weave exactly what you had in mind!
-
-
We are also happy to discuss making your bespoke tweed into products either for you to sell on or for yourself. These are costed on an individual basis based on the items and quantities required. Bare in mind that we are a very small team of three sisters and cannot do large bulk orders!
-
-
Please note we do not, and cannot weave Harris Tweed due to the mill being unwilling to reliably supply yarn or finish (wash) our tweeds
-
-
Here are examples of commissions we have done in the past;
Here the customer wanted an overcoat and matching waistcoat made in his own unique tweed. We did actually weave less than 30 meters in this instance as we wove the rest of the warp in a different colour for our own use. The customer chose the three warp colours and the fantastic contrasting orange weft, then designed the coat and waistcoat with me and I made it to his specifications.
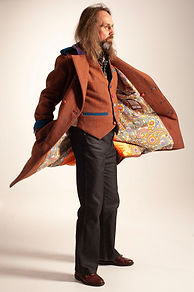
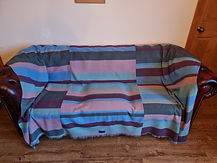
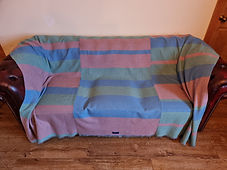


This collection of blankets was ordered as gifts for the couples children, woven in their school colours. This is merino yarn so beautifully soft for snuggling under! I even hand embroidered their initials on them
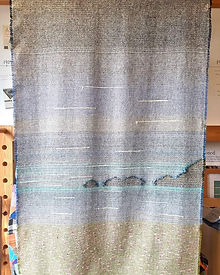

We can even weave wall hangings to order to look like a landscape special to you. We can create (to an extent) mountains and rocks etc. add different colour "flowers" and generally personalise. These are the most difficult to acheive as they are abstract and not an exact rendering of the photo. Where the shaped sections are will often be wee gaps but since it is a wall hanging these all become part of the charm of being woven on such an old loom!
This beautiful blue-faced Leicester yarn belonging to the customer was spun and dyed by our usual mill The Border Mill. We had a slight hiccup as the customer hadn't asked us what quantities were needed for the pattern they originally wanted before ordering the yarn so we had to modify the design based on the available colours and quantities. But it turned out absolutely stunning - I'd have happily kept it!




My biggest commision to date - this was for the Scottish Travel Society, two 60 meter rolls of tweed in their own unique design. I sold the products on my own website and made them to order for their members. Over 200 scarves plus shawls, throws and more!

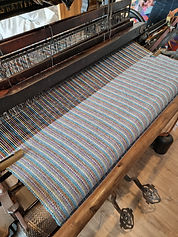

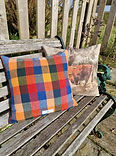
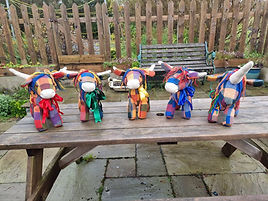
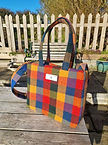
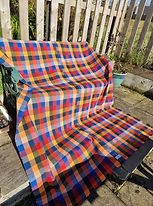
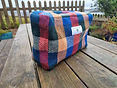
This commission was a big one! 30 meters of tweed woven in a block check in the customers colours, which I then turned into blankets, cushions, scarves, bags, heilan coos and a unicorn!
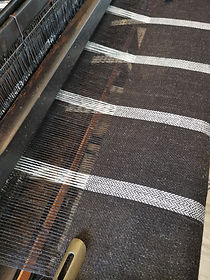

Woven in the customers own Hebridean yarn with accents of Shetland this tweed I turned into a collection of throws for the customer to sell in their shop
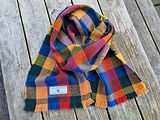
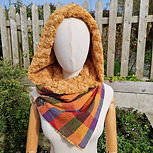

This customer has ordered two years in a row! This sublime yarn is from Icelandic Leader Sheep and is incredible to work with. It was very finely spun so created a lovely lightweight warm cloth. We wove four rolls in the various colourways to showcase the different sheep colours.
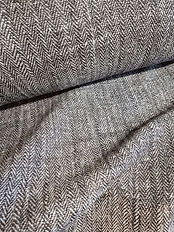.jpeg)
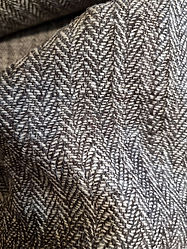.jpeg)
